<span style="font-weight: bold;">Today, images and news of under construction infrastructure projects compete for popularity with politics, cinema and cricket in the popular discourse.</span>
<p></p>
<p></p>
<p><span style="font-weight: bold;">INFRASTRUCTURE TODAY </span>recently caught up with<span style="font-weight: bold;"> Kapil Bhati, Managing Director, Robbins Tunneling and Trenching Technology India</span> to get a sense of the growth of the excavation construction machinery in India. Bhati says that the segment will continue to expand over the next decade.</p>
<p> <span style="font-weight: bold;">What are some of the areas that have witnessed an exponential growth of the tunneling business?</span><br />
Not only now but there will be a huge requirement for the tunneling business over the next ten years. With the completion of the first phase of metro projects in major cities, the second phase of the project is in the pipeline. Then, Tier II cities are also going in for metro projects. Road tunnels of the size of 12-14 metre diameter are being looked at. Interlinking of rivers is another important area on which the work is already underway. A couple of such projects are already in the pipeline and there are more that have been studied, evaluated and are going to be tendered out very soon. The size of such tunnels would be 10-12 m in diameter and the length would be anywhere from 50-70 km. Work on tunnels at hydroelectric projects that was slow in the past has since now been revived. A couple of hydroelectric projects in North India offer immense potential. A few more projects are also coming up. Therefore, a few hundred kilometres of tunneling would be required every year. </p>
<p> <span style="font-weight: bold;">Tell us about some of the most noteworthy projects that you have undertaken so far?</span><br />
One of the challenging projects that we took up is in Telangana, for a 10 m wide and 43 km long irrigation tunnel. The entire length of the project was to be done using only two machines from each side. So far, we have already completed 30 km of the projects. There were ground challenges in between that we have successfully overcome. The machine components were not designed for the project. Even the main bearing which is the heart of a tunneling machine has the lifespan of 7,000-10,000 working hours and those got completed faster. Consequently, we had to change the main bearing inside the tunnel by making a niche. Once the project is completed, it would be the longest tunnel in the world with no intermediate access. We have also worked on some more difficult projects in India. We had undertaken a job in the Parvati Valley in the Indian Himalayas and successfully encountered all topographical uncertainties. While tunneling for the Bengaluru Metro, the Tunnel Boring Machines (TBM) often came across abandoned wells filled with old metal parts and water table with old construction overground. </p>
<p> <span style="font-weight: bold;">What kind of attendant services do you provide with your machines?</span><br />
When we had newly entered the Indian market, we were often asked as to how we would support our technology. We did that by providing experts and crews to the contracting companies. We are now the only company in India that takes the full responsibility for a contract. That means, other than providing the machine, we execute the entire job with our crew. Or to put it more simply, we supply the machine and also take up the job on a per metre basis. </p>
<p> <span style="font-weight: bold;">You had an interesting experience while you were tunneling near the heritage structure of Chand Pol (Moon Gate) in Jaipur Rajasthan. Tell us about that experience.</span><br />
The underground section of Jaipur Metro was won by Taiwan’s Continental Engineering Corporation (CEC). We agreed to supply the machine as well as extend operational support. However, we soon realised that the point from where the boring was to commence was barely 100 m from the heritage structure of Chand Pol. The foundation of the gate to the crown of the TBM was only 6 m. Usually, a minimum of 1-2 m of clearance is required above the crown of the machine but then Chand Pol being a heritage structure, this was a big challenge. We were given the full responsibility for execution of the project by CEC and stationed our most experienced crew there. Any damage to the site would have spelled legal trouble for us. But our foreign and Indian crew took up the challenge and operated those machines with a rare precision and tolerance. We eventually managed to bore two tunnels with a tolerance of 2-4 mm with no impact to the heritage structure. </p>
<p> <span style="font-weight: bold;">At a time when several big-ticket infrastructure projects are on in the country, do you also observe any change in the attitudes at the administrative level as far as service providers like you are concerned?</span><br />
If we compare with the past, these days the decision-makers are a lot less apprehensive. Clear targets are given to teams and they work on solutions with the right attitude. Tunneling projects with a high difficulty level in roadways, hydroelectric dams and river linking are being executed at a pace that couldn’t be imagined earlier. The authorities too display a positive attitude and are more understanding of the challenges. Tenders and other project documents are compiled based on discussions and suggestions from all stakeholders.</p>
<p> <span style="font-weight: bold;">Have you noticed any fast-tracking of projects on the part of the federal or state governments?</span><br />
Definitely, clear targets and timelines are given to the authorities at the central and state level. One can sense a certain sense of urgency in the discussions, tendering and awarding of project contracts. </p>
<p> <span style="font-weight: bold;">What new regions of the country are you looking at in the near future?</span><br />
We are presently executing a job in the Himalayas (Nepal) that involves a 12 km-long tunnel. With this project, we have achieved the best production rate in Himalayas of 1 km in a month. Our machine bores at the rate of 600 m in a month, which is a significant achievement in the Himalayan conditions. It proves that with the observance of specific precautions and implementation of certain suitable features in the machine, and the right crew, one can successfully carry out boring operations even in the very challenging Himalayan region. There are a few projects in the tendering stage for the Indian Himalayas. We have provided our expert opinion to our client on the specifications that need to be implemented in the machine itself to meet any challenge that might arise at the execution stage. We are delighted to note that the client readily understood, accepted and incorporated those features in the tender document. Negotiations are in the final stage and should hopefully close soon. </p>
<p> <span style="font-weight: bold;">You are reportedly also looking at railway projects in the Uttarakhand Himalayas with immense interest.</span><br />
Indian Railways’ subsidiary, the Rail Vikas Nigam (RVNL) was given the special task to set-up a rail link from Rishikesh to Rudraprayag. We have been closely working with them and surveyed the geology and made some suggestions after discussing with our engineering team. Preparations are on a full-swing and are now almost in the final stage. Tenders will soon be issued for over 100 km of tunnels from Rishikesh to Rudraprayag. Once the project is concluded, the accessibility to the pilgrimage sites would improve immensely. We are already associated with the contractors bidding for the job and it is going to be a major upcoming contract.</p>
<p> <span style="font-weight: bold;">Are you able to source the right kind of people to operate your highly specialised machines within India?</span><br />
When we started operations here, we initially brought a foreign crew. Like for one of our projects, we had 14 expatriates operating one machine with a very small number of Indians in the team. At that time, it was my personal target to create an all-Indian crew. We started hiring fresh engineering graduates and trained them on our machines. We took the finest to places, like the US, to provide them with additional specialised training. Today, I am happy to say that the same machine that was being operated by a large team of expatriates, has only three foreign nationals, with the majority of the crew comprising of Indians. </p>
<p>We now have nearly 300 experts on our payroll who not only operate our machines but also those of our competitors in the times of need. Also, we now have Indians supporting Robbins’ overseas projects in Singapore and Australia at the same level and salaries as those of expatriates. </p>
<p> <span style="font-weight: bold;">The government has been emphasising a lot on Make in India. Are you looking at setting up facilities to manufacture TBMs here?</span><br />
In 2006, when we first brought two of our machines to India, 30 per cent of their parts were locally manufactured. Since then, any machine supplied here has a substantial number of its parts manufactured locally. Only critical components such as big size bearings and drive motors are sourced from overseas. However, parts related to sheathing, backup structure, ventilation, railway track and California systems, are all made here. In less than a year’s time, we will be setting up an assembling and testing unit near Mumbai. The facility will have machines imported from Singapore that will be readily available to anyone who needs them. One of Robbins’ core philosophy is to give back to the country where we have a presence. Therefore, we try to source most manpower as well as parts locally. </p>
<p> <span style="font-weight: bold;">- MANISH PANT</span></p>
FlashNews:
India Plans Airport-Centric Real Estate Push; Naidu Targets 15% Economic Growth
NALCO’s Lithium Leap: Head Reveals Timeline for Argentina Mines, Global Expansion Plans
Mumbai-Ahmedabad Bullet Train Gains Momentum with Major Civil Works Milestones
ONGC Begins Gas Sales from Chinnewala Tibba Block, Boosting Rajasthan’s Energy Grid
OIL-BPCL Join Hands for City Gas Network Rollout in Arunachal Pradesh
Government push makes India’s maritime sector future-ready, unlocking $1 trillion potential”: Sonowal
ISRO Innovations Continue to Reach Industry as IN-SPACe Signs Five New Deals
India Launches Maritime Hackathon at IIT-Madras to Power Port-Tech Startups Ahead of Maritime Week 2025
CAE, InterGlobe JV Opens Fourth Commercial Aviation Training Centre in India to Meet the Country’s Soaring Pilot Demand
India’s Space Vision 2040: Jitendra Singh Says Astronaut Will Announce ‘Viksit Bharat’ from Moon
India May Launch Dedicated Maritime Satellite to Boost Coastal Governance: Sonowal
Modi Inaugurates ₹18.7 Billion Aunta-Simaria Ganga Bridge to Link North and South Bihar
Biofuels Earn Farmers $15 Billion Over 11 Years, Says Puri; Reaffirms Commitment to Shield Consumers from Fuel Price Volatility
Reacting to Trump tariffs, India, Brazil expand oil ties: S&P Global Commodity Insights
Jupiter Wagons Secures $25.8 Million Vande Bharat Wheelset Order, Plans Major Odisha Expansion
WABAG Wins $5.6 Million Water Management Contract for RenewSys Solar Cell Facility in Hyderabad
IHCL to redevelop historic Chotelal Ki Ghat in Kolkata under heritage-led riverfront initiative
India’s Airline Profitability to Dip Amid Airspace Disruptions and Safety Concerns: Crisil Ratings
Welspun One Expands South India Warehousing Portfolio with $258 Million Investment
Home » India would require a few hundred kilometres of tunneling every year
India would require a few hundred kilometres of tunneling every year
ECONOMY & POLICY
October 31, 2018June 9, 2021
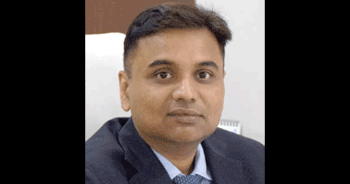
Leave a Reply
You must be logged in to post a comment.