The road construction companies are eying 20 per cent growth through this fiscal. With this, a plethora of opportunities have opened up for road equipment industry. That said, looking at the pace at which the road construction is progressing in the country, the road equipment segment sees a considerable demand in the future.
<p></p>
<p> Fiscal 2018 was particularly frenetic, with 17,000 km road projects- the highest ever in a year- being awarded by both the Ministry of Road Transport and Highways and NHAI. The pace of construction, at 27 km per day, was twice that of fiscal 2014. And over 90 per cent of these contracts were based on the hybrid annuity (HAM) and EPC models. The construction is expected to accelerate to 32 km per day by 2020 given NHAI’s sharp focus on the award of projects under the Bharatmala programme. More than half of these are expected to be under HAM. That said, looking at the pace at which the road construction is progressing in the country, the road equipment segment sees a considerable demand in the future. </p>
<p>In an interaction with <span style="font-weight: bold;">CONSTRUCTION WORLD, Ramesh Palagiri, Managing Director and Chief Executive Officer, Wirtgen India </span>believes that pavers and compactors have had a good run in recent years on the back of buoyant road construction. ‘Over the past three years, the demand for compactors has doubled to 5,000 units per annum while the demand for sensor pavers has registered a modest increase to 3,300 units per annum,’ he says. </p>
<p>Wirtgen India is offering the Vogele range of sensor pavers in India. Vogele has been the industry pioneer as well as the market leader for asphalt pavers. ‘The Vogele range of sensor pavers can pave from 1.5 m paving width to a maximum of 16 m- the widest range,’ claims Palagiri. </p>
<p><span style="font-weight: bold;">Dimitrov Krishnan, Vice President and Head, Volvo CE India</span> spills the beans on how the government’s plan will benefit the road equipment industry. ‘With an investment of Rs 7 trillion to build 83,677 km of roads in the next five years and to increase the road construction from about 23 km a day to 40 km a day, have made road pavers, particularly sensor pavers, increasingly important,’ says Krishnan, who expects 20 per cent growth in soil, asphalt and mini-tandem sales in 2018, and 15 per cent growth in paver sales. Volvo CE, a global player in pavers which has a manufacturing facility in India, offers tracked pavers (P6820C ABG and P5320B ABG) and wheeled pavers (P4370B ABG).</p>
<p>Echoing the similar sentiments,<span style="font-weight: bold;"> Rajinder Raina, General Manager, Escorts Construction Equipment</span> puts some numbers to substantiate the claim. ‘In the last fiscal, vibratory compactor sales crossed 5,000 units, valued at over Rs 10 billion, while in the past few months, sales crossed more than 500 units on a back-to-back basis, a first for the country,’ notes Raina. </p>
<p>’Of all the infrastructure sectors driving demand for compactors- comprising of roads and highways, mining, real estate, power, railways- the leading sector is currently roads and highways with many large-scale projects being implemented,’ says Jasmeet Singh, Head-Corporate Communications and Corporate Relations, JCB India, which offers three world-class products in road construction solutions: the VMT330 (a 3T-class mini tandem roller), the VMT 860eco (a 9T-class tandem roller) and the JCB116 (a 11T-class soil compactor). </p>
<p>According to Ajay Aneja, Brand Leader, CASE India, vibratory compactors accounted for 96 per cent of compaction equipment sales owing to their high compaction force, reliability and cost-effectiveness. Within this, he includes both soil and tandem vibratory compactors, which CASE India caters to with its 1107EX, 1107 EX-D, 1107EX-PD vibratory soil compactors, 450 DX vibratory mini-tandem compactor and the newly released 752 EX vibratory tandem compactor. Whereas mini compactors comprise 6-8 per cent of the volume, the balance is shared by soil and tandem vibratory rollers in the ratio of 60:40, respectively, reckons Raina.</p>
<p>’Demand for soil compactors and tandem rollers go together; you need both for road widening projects,’ opines Singh. ‘For a smaller span, the JCB mini-tandem roller is a perfect fit.'</p>
<p>’Static rollers are (mostly) used by small contractors for the repairs and maintenance of minor roads,’ notes Aneja. ‘Last year, this category comprised about 3 per cent of the compaction equipment market.’ Pneumatic tire-rollers are mostly used for surface sealing, an application generally limited to major roads and highways, adds Aneja, where these accounted for the balance 1-2 per cent.</p>
<p>While most Indian users prefer 10-11 tonne soil compactors to meet government norms and achieve the requisite compaction, Raina expects a surge in demand for soil compactors of capacity greater than 11 tonne, capable of better or deeper compaction, driven by the increase in the load-bearing capacity of vehicles expected to ply on new roads, while 10 tonne compactors will continue to be demanded for state and rural roads, irrigation canal works and sundry jobs.</p>
<p> <span style="font-weight: bold;">Mechanical vs sensor pavers</span><br />
Mechanical pavers are the most economical and efficient solution while sensor pavers are advanced pavers with intelligent monitoring systems. Mechanical pavers, though economical, cannot provide a smooth finish to the surface. In turn, this affects the traffic flow of the highway and increases maintenance requirements in the finished road. Sensor pavers have intelligent operating technology that helps control the machine in terms of mat thickness as well as the level of the mat and the grade required for the finished road. </p>
<p>Krishnan elaborates on the advantage of sensor pavers over mechanical pavers, ‘The paving quality of any road is defined by the ability of the paver to satisfy three requirements in line with the highway design: mat thickness, level of the mat and the grade required. Regular pavers without sensors simply follow the undulations of the road base and are therefore, unable to give a smooth finish to a paved surface. But sensor pavers have intelligent operating technology that helps the machine deliver on these three requirements.'</p>
<p>Palagiri echoes the same as he says, ‘In the highway segment, the use of sensors pavers play a very important role in getting the right levels and grades when building the roads. </p>
<p>The final finish of the road depends, to a great extent, on the accuracy delivered by these pavers, in addition to the mix quality and temperature at which it is laid and also compaction.'</p>
<p> <span style="font-weight: bold;">Tippers and dump trucks</span><br />
With many road projects going ahead, demand for trucks for the surface transportation of aggregates will get a boost, states <span style="font-weight: bold;">Rajesh Kaul, Product Line Head, M&HCV, CVBU, Tata Motors.</span> ‘Higher surface movement means higher migration to bigger vehicles.’ In mining, ‘Primary minerals such as coal, iron ore, bauxite and limestone will continue to represent most of the equipment purchase, transport and otherwise,’ opines Rama Rao AS, Executive Vice President, Sales, Marketing and Aftermarket-HD Trucks, VE Commercial Vehicles.</p>
<p>’Better utilisation of coal-based thermal power plants is likely to improve the need for transportation of coal via road but other mining segments have seen slow growth,’ adds Kaul.</p>
<p> <span style="font-weight: bold;">Choosing a truck</span><br />
The truck preference of buyers depends on the application, the geography (terrain) where it will ply and the nature of work, states Kaul, explaining: ‘Shorter vehicles offering better manoeuvrability are the preferred choice for hilly terrain and mining applications. Longer vehicles with configurations of 8 and 10 are deployed for surface transport applications. </p>
<p>The longest of all tip trailers offering larger load bodies and higher carrying capacities are being used for very long leads on broad national highways.'</p>
<p>’Users invest in dump trucks or tippers depending on the quantity and scope of work they have in hand,’ says <span style="font-weight: bold;">Ranjit Ravindran, Business Head, Mining, Mining & Construction Equipment Division, Voltas.</span> ‘Typically, they prefer tippers where the quantum of earth or ore removal is likely to take three to four years while dump trucks make sense for large-scale mining spanning a decade or more. The quantity of the reserve must justify the investment in the dump truck.'</p>
<p>Typically, customers choose a dump truck or tipper-based on the capacity of the bucket of the loading equipment, which can be a rope shovel, hydraulic excavator or wheel loader, says <span style="font-weight: bold;">Rama Rao AS, Executive Vice President, Sales, Marketing and Aftermarket-HD Trucks, VE Commercial Vehicles.</span> ‘For optimum productivity, the industry standard is to fill the haulage equipment in four passes of the loading equipment.’ </p>
<p> <span style="font-weight: bold;">Preferred trucks</span><br />
Indian users prefer 30-35 tonne payload tippers and 35-100 tonne payload rigid dump trucks, informs <span style="font-weight: bold;">Ashim Kumar Mukherjee, Technical Advisor, Enrika.</span></p>
<p>In the off-highway segment, 60 tonne and 100 tonne dump trucks are most preferred in India, says Ravindran. ‘Fewer users such as Coal India, NTPC, Reliance and Hindustan Zinc have extensive operations that justify an investment in ultra large-sized dump trucks of 240 tonne capacity.'</p>
<p>’Coal India and its subsidiaries extensively deploy 65 tonne and 100 tonne dump trucks, the most popular class in India, while South Eastern Coalfields and Reliance deploy 240 tonne dump trucks in combination with large electric rope shovels of 42 cu m capacity,’ shares Mitra. ‘Private operators getting into mining are making tippers more popular for coal evacuation.’ That said, a shift in demand towards higher capacity trucks seems to be underway. </p>
<p>Mitra notes a surge in demand for 150 tonne, 190 tonne and 240 tonne dump trucks, which he ascribes to the increasing stripping ratio in mines and more overburden having to be handled to expose coal, as a result of which coal benches are becoming taller. This leads to the deployment of higher capacity loading equipment, thereby increasing the capacity of the haulage equipment. </p>
<p>With recent mining leases period going up to 25-30 years in some cases, Mitra is very hopeful that the capex on higher capacity equipment would be justified and these would be deployed more frequently. ‘Large capacity equipment would substantially increase productivity and contribute to safer operations by reducing the number of mobile equipment in the mines,’ he adds.</p>
<p> <span style="font-weight: bold;">Market perambulations</span><br />
The construction equipment industry is today pegged at USD 4.3 billion in value with the Feedback Business Consultancy report forecasting industry volumes to spike upto over 120,000 units by 2021 growing at a CAGR of 20 per cent. The current industry volumes are close to 75,000 units. Policy changes in the infrastructure segment are expected to boost the equipment industry to an estimated USD 7.5 billion by 2020. Loaders, excavators and compactors dominate the road sector with backhoe loaders singularly contributing the largest chunk of the sales pie. In China, this segment chips in with 0.5 per cent sales while North America accounts for just 8.5 per cent. Key players in the fray are Tata Hitachi, Kobelco, Hyundai, Case New Holland and JCB with most of the machinery sporting a local content of 60-70 per cent. However, some international players like Caterpillar and Kobelco Construction Equipment continue to import a larger component basket.</p>
FlashNews:
Biofuels Earn Farmers $15 Billion Over 11 Years, Says Puri; Reaffirms Commitment to Shield Consumers from Fuel Price Volatility
Reacting to Trump tariffs, India, Brazil expand oil ties: S&P Global Commodity Insights
Jupiter Wagons Secures $25.8 Million Vande Bharat Wheelset Order, Plans Major Odisha Expansion
WABAG Wins $5.6 Million Water Management Contract for RenewSys Solar Cell Facility in Hyderabad
IHCL to redevelop historic Chotelal Ki Ghat in Kolkata under heritage-led riverfront initiative
India’s Airline Profitability to Dip Amid Airspace Disruptions and Safety Concerns: Crisil Ratings
Welspun One Expands South India Warehousing Portfolio with $258 Million Investment
India Post Launches $700 Million Digital Overhaul with Advanced Postal Technology Rollout
Suzlon Commits to 100% Renewable Energy Across All Manufacturing Units by 2030
Inox Wind Divests ₹1.75 Bn Stake in EPC Arm at ₹74 Bn Valuation
Air India and IndianOil Sign SAF Supply Pact to Advance Net-Zero Aviation Goals
New HAM Bidding Norms May Sideline 25% of Road Developers, Says Crisil Ratings
INOX Wind Posts Record Q1 Profit, Strengthens Growth Outlook
Genesys International Q1 Profit Surges 32% on Strong Mapping Demand
Asia-Pacific to Drive 33% of Global Regional Jet Demand by 2045: Embraer
India Achieves 100 GW Solar PV Milestone with ALMM-Driven Expansion
Air India Accelerates $400 Million Fleet Retrofit Programme Across Widebody and Narrowbody Aircraft
ONGC Q1 FY2026 Net Profit Rises 18.2% to ₹115.5 Billion on Strong Gas Realisations and Offshore Gains
Centre Defends Ethanol Blending Programme Amid Mileage Concerns; Highlights $16.5 Billion Forex Savings
Home » Paving the Way
Paving the Way
Roads & Highways
September 1, 2018June 9, 2021
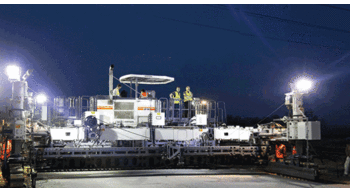
Leave a Reply
You must be logged in to post a comment.