Construction efforts are being subject to mockery through the use of inferior quality TMT rebars. CONSTRUCTION WORLD investigates with analysis from FIRST Construction Council…
<p></p>
<p> The infrastructure sector is highly responsible for propelling India’s overall development. With intense focus, the government has initiated policies to ensure time-bound creation of world-class infrastructure in the country. In this year’s Union Budget, Rs 5.7 trillion has been allocated for infrastructure.</p>
<p>The government plans to build 50,000 km of roads worth USD 250 billion by 2022, of which Rs 1 trillion will be spent during 2018-20. A total of 189 port modernisation projects involving an investment of USD 22 billion by the year 2035 has been envisioned. Housing is a major opportunity in terms of growth. The Indian real estate market is expected to touch USD 180 billion by 2020. Affordable housing alone is an opportunity worth Rs 6.25 trillion by 2022 for which an additional 25 million units will be needed. Considering that the average cost of such houses is Rs 2.5 million, the opportunity is worth Rs 6.25 trillion.</p>
<p> <span style="font-weight: bold;">Increased Capacities of Allied Industries </span><br />
With such kinds of investments in infrastructure, even allied segments like steel and cement industries have witnessed expansion. The figures illustrate how steel production capacities in India has gone up from just 14.23 million tonnes (MT) in FY92 to more than 100 MT currently.</p>
<p>Similar is the scenario of the cement industry in India, whose current manufacturing capacity stands at 455 MT, up from 161 MT in FY2007. With increasing spending on infrastructure, the capacities are expected to scale up even further. </p>
<p>While the capacity of the cement sector is expected to touch 550 MT by 2025, for the steel sector, recently unveiled new steel policy by the Government of India envisages the annual steel consumption at 300 MT per annum by 2030. This is three times that of the current consumption of 100 MT per annum. </p>
<p> <span style="font-weight: bold;">Quantity or Quality:</span> Where Are We Heading? With the above parameters, we want to indicate that infrastructure development has resulted in many changes (for better) like rapid urbanisation, improved standard of living and last mile connectivity. And, it is no wonder that it has resulted in a major shift in housing. </p>
<p><span style="font-weight: bold;">Corollary to this, we would like to ask a simple question:</span> Are we really paying attention to quality in infrastructure? How has the quality of materials been in the overall infrastructure? Quality gains more prominence in an era where the built infrastructure has to be created in a short span of time, with all the ability to sustain loads much higher than what they are meant for. In simple terms, the speed of road construction is important for the GDP growth, but the quality is needed to ensure sustainability and to keep the O&M costs under control in the longer term. </p>
<p>Adding to that, events like accidents, breakdown of bridges, buildings and overall infrastructure are now subject to harsher and more unpredictable environment. Events such as Kolkata bridge fall, foot-over-bridge collapse or caving-in of a car parking wall in Mumbai, accentuate the dire need for the use of better quality of raw materials. In fact, they underscore the lack of technical intelligence in the procurement department, which does not pay heed to acquiring good quality raw materials and places more emphasis on cutting costs. </p>
<p>Hence, while in quantitative terms, India has seen a significant improvement; it is a matter of introspection: How are we placed on qualitative parameters? </p>
<p> <span style="font-weight: bold;">Time to Understand: Inherent Strength </span><br />
If the base of any product is of low quality, the quality of its derivatives will also be low. In infrastructure, while a lot has been researched, written and spoken about raw materials like cement, paints, stones and other accessories- all visible materials- there is hardly any research available on reinforcement bars (rebars), also known as thermo-mechanically treated (TMT) bars. Rebars form the backbone of any reinforced cement concrete (RCC) structure- be it the foundation, column, beam or slab- and their quality is critical in defining the overall quality of the structure.</p>
<p>Rebars are used in RCC constructions varying from large infrastructure projects like bridges, ports, airports, urban infrastructure, industrial plants and commercial buildings to small RCC-based individual house construction. TMT bars are the backbone of civil constructions. They are deeply anchored into concrete to bear the loads of buildings, slabs, beams and columns, along with the load of people and their belongings. They should be able to withstand the furies of nature, such as windstorms and earthquakes. The consumption of rebars in India is currently estimated at about 24 MT/annum, valued at approximately Rs 1.2 trillion.</p>
<p> <span style="font-weight: bold;">Importance of Rebars</span><br />
Looking at the Rs 1.2 trillion annual market, not many would consider rebar as an important element in infrastructure. However, considering the average steel intensity of about 10 per cent by value in an RCC construction in India, the total construction industry can be valued at 10 times the valuation of the rebar industry, which works out to an astronomical Rs 12 trillion per annum. These are current figures and with infrastructure projects planned till 2025 or 2030, the figures are expected to swell in multiples. With such a large construction industry being critically dependent on the quality of steel rebars used, it is imperative that all efforts are made to produce and promote the use of good quality rebars in India.</p>
<p>Are we really making good quality products in the rebar industry? The answer is, while we speak about the quality in the rebar sector, there is already a bifurcation, namely, primary and secondary quality rebars. While the primary players enjoy 45 per cent of the market share, the secondary players enjoy 55 per cent.</p>
<p>Primary steel is acquired from a steel-making method, known as the converter process. Here, iron ore is converted into steel. This process uses pig iron from the blast furnace. </p>
<p>Secondary steel is usually made after adding some alloying elements to the primary steel, often by melting scrap or sponge iron, and sometimes a mixture of both. A little ahead in the story, we shall explain the difference between primary and secondary manufacturers. Before that, let’s understand if there are any standards imposed on the manufacture of secondary steel.</p>
<p> <span style="font-weight: bold;">Are There Any Standards Imposed?</span><br />
No one would deny the fact that all good recipes start with quality ingredients. So the quality and strength of a structure depends on the quality of steel used in the construction. In India, BIS 1786 is a compulsory standard for steel. Steel of optimum quality can only be manufactured by using good quality raw materials and reliable rolling process. Even if one of these parameters- the raw material or the manufacturing process- is weak, the quality of finished steel will not be at par with the standards mentioned in the BIS specification (BIS 1786, Amendment 3, 2018). </p>
<p>The Ministry of Steel (MOS) as well as the Bureau of Indian Standards have been instrumental in bringing about a change in terms of the quality of steel being produced in the country. The key focus of their earlier and current endeavours has been on the beneficiation of the consumer. For example, mandatory BIS certification for all grades and sizes, steel quality control order, minimum import prices, safeguard duties and anti-dumping duties have been some of the key steps taken by MOS and BIS to keep a check on quality and regulate the supply of spurious material into the country.</p>
<p>But despite the steps being taken by the MOS and BIS, we still have a few players who manufacture secondary quality steel. Rather, the market share of the secondary players is higher than that of the primary players. What is surprising is that the spend on branding by the secondary players seems to be higher than that of the primary players. If the number of commercials aired on the national-level television by secondary rebar players are anything to go by, it indicates so.</p>
<p> <span style="font-weight: bold;">Prime Difference: It Is the Process That Matters</span><br />
It is important to differentiate between primary and secondary manufacturers. To understand the difference, one has to understand the process of steel manufacturing. This process flow chart can be simplified for the uninitiated to understand the various stages and methods of steel-making and finished steel.</p>
<p> <span style="font-weight: bold;">Process: What’s Missing, Rather What’s Present?</span><br />
As per the simplified version, the process is as follows: the first step is to select the right raw material, keeping in mind that if the base is of low grade, the end product cannot be expected to be any better. In the first step itself, the differentiation starts. Primary players use iron ore, coking coal, limestone, pellets and sinter. But, secondary players use scrap of direct reduced iron (DRI), usually purchased from the primary players (which is not utilised by many primary players). While scrap already means low grade, DRI is highly susceptible to oxidation and rusting, if left unprotected and is normally quickly processed further to steel. Bulk iron can also catch fire since it is pyrophoric. Unlike blast furnace pig iron, which is almost pure metal, DRI contains some siliceous gangue, which needs to be removed in the steel-making process.</p>
<p>While the first step is a problem with the secondary players, the most important second step of the blast furnace is missing in the process of making iron among secondary players. Hot metal produced by the blast furnace gives the purest form of iron for further conversion to steel. Missing this stage leads to a lot of impurities remaining in the product. It is a matter of worry that these impurities eventually affect the quality of the finished product. </p>
<p>Even in the third step, primary players use basic oxygen furnace of EAF, where initial refining takes place and elements like carbon, silicon and manganese are controlled. Again, no such control is present in induction furnace, which is used by the secondary players.</p>
<p>Further, refining occurs in the primary stage where harmful elements like phosphorous and sulphur are controlled. While we call them as harmful elements, they are the necessary evils. Despite being harmful, certain amount of their presence is necessary. We have provided a table in which the maximum content of those elements are mandated as per BIS 1786. </p>
<p> <span style="font-weight: bold;">Importance of Refining Compulsory Evils: The WTC Story</span><br />
Everyone remembers the attack on the World Trade Centre (WTC) in 2001. When WTC had caught fire, its steel melted (like any other steel generally would have). However, the test results showed that it collapsed a bit early and imploded due to higher sulphur content. It is still debated if the sulphur was present in the steel or it was added due to the other burning particles around the building. However, the bottom line is that higher sulphur content in steel makes it melt much earlier than steel having controlled content of sulphur. </p>
<p>There is an important connection between concrete and steel. In any construction, RCC and steel are the two most important factors. Rather, it is the fusion of both that makes it a perfect combination. RCC has a great compressive power but relatively low tensile strength and ductility. Therefore, when it fuses with TMT steel bars, it gives rise to a highly ductile and tensile combination. Hence, it is important to understand how ductile and tensile combinations are measured and tested.</p>
<p>While understanding the chemical composition, it is also important to understand three important aspects, namely, yield strength, UTS/YS ratio and elongation (%). While yield strength defines the minimum limits of load that can be applied to steel without having any deformation, the UTS/YS ratio defines the energy absorbed by the steel bar. In simple layman terms, UTS/YS ratio signifies the time duration that one gets for evacuation before the failure of steel. </p>
<p>The yield strength or yield point of a material is defined in engineering and material science as the stress at which a material begins to deform plastically. Prior to the yield point, the material will deform elastically and will return to its original shape when the applied stress is removed. Once the yield point is passed, some traction of the deformation will be permanent and non-reversible. Then comes the ultimate tensile stress (UTS)- the amount of tensile (stretching) stress a material can withstand before failing or breaking. Here, the most important factor is UTS/YS. </p>
<p>Imagine a situation when there is an earthquake, fire or other calamity- the inherent tensile and ductile strength of quality TMT bars provides sufficient time for safe evacuation of people. </p>
<p>In structural applications, catastrophic failure from exceeding the UTS should be considered extremely bad. A high number of casualties can occur when a structure fails with no warning that it is being overloaded. The ability to see components starting to yield can give occupants a warning, allowing them to evacuate. Also, when one component of the structure fails, it can transmit shock and impact loads to the other components of the structure; if the peak of these loads also exceeds the UTS of those other components, a single failure can cascade into even greater damage. If the material can yield and deform significantly before failing, it can absorb the impact energy and prevent it from being transmitted else where.</p>
<p>While there would be many other stories that would make one understand how the evil contents affect the quality, we must first understand how the manufacturers of secondary steel emerge.</p>
<p> <span style="font-weight: bold;">How Clusters of Secondary Players Emerge</span><br />
Here is the root cause of the emergence of secondary players. In the absence of blast furnace, there is a humongous difference between the capex required for setting up primary plants and secondary plants. To quantify, while the capex needed for a primary manufacturer is around USD 1 billion, it is just USD 1 million for a secondary player. </p>
<p>As it is not feasible for rebar manufacturers to cater to markets which are more than 200 km from the manufacturing facilities (due to heavy weight adding to the freight cost), there are clusters created by secondary manufacturers. With lower capex requirement, these players create smaller facilities around the raw material sources and even around the markets they want to cater to. Now, the primary players have lesser number of plants and though they produce a quality product catering to the larger or pan-Indian markets, is not feasible. With a demand-supply mismatch, there is a natural emergence of secondary players who hardly spend on capex for quality TMT production. </p>
<p>There are about 16 clusters in India that are closer to places where raw material is available and markets to cater to. While a few have appeared around ship-breaking yards (as ship scrap is available abundantly and obviously at cheaper rates). A few clusters are also developed near scrap collection yards. Overall, clusters mostly appear near places with low quality raw material availability. The figure indicates that the Indian clusters can be divided into two parts. It also illustrates how there is a 80:20 ratio of scrap:DRI in one part, and again a 80:20 ratio of sponge iron:DRI in another.</p>
<p> Some clusters of secondary producers:<br />
1. Mandi Gobindgarh (near Ludhiana)<br />
2. Ghaziabad, Muzaffarnagar (West UP)<br />
3. Kotdwar (Uttarakhand)<br />
4. Jaipur/Bhiwadi<br />
5. Kanpur/Lucknow<br />
6. Raniganj<br />
7. Durgapur<br />
8. Raipur<br />
9. Jalna (Maharashtra)<br />
10. Bhavnagar (Gujarat)<br />
11. Erode (TN)<br />
12. Rourkela </p>
<p> <span style="font-weight: bold;">How Much Are We Risking and At What Cost? </span><br />
In the absence of blast furnace, the manufacturing cost ratio would be 3:4 in favour of the secondary players. A secondary player can manufacture (lower quality) TMT at just three-fourths of the cost of the primary players. While such is the difference in cost, in times of lower capacity utilisations, it is the primary player who suffers more as the operating leverage reduces significantly. On the pricing front, while the different rates are available in different sectors, there is clear difference of Rs 6,000-8,000 per tonne. If the primary rebar is available at Rs 48,000 per tonne, secondary rebars are available at around Rs 40,000-42,000 per tonne. </p>
<p>Let’s calculate the cost of rebars required for constructing a 1000 sq ft house. Consider that, at 3 kg per sq ft (including beams, columns and pillars), the total rebar requirement is around 3 tonne. The cost for using primary bars will be around Rs 144,000. Similarly, for using secondary rebars, the total cost stands at around Rs 120,000. It is just a matter of Rs 24,000 for which we are risking the strength of our house structure. Considering a construction cost of Rs 3000 per sq ft, the total cost is around Rs 3 million. It means, the cost saved is just Rs 24,000, which is a mere 0.8 per cent of the construction cost. Consider the land cost, we are just saving 0.6 per cent of the total house cost.</p>
<p> <span style="font-weight: bold;">Need for end-users to step in </span><br />
The worst case is that the end users are spending almost Rs 1,50,000 for TMT.Despite paying such a huge cost for the product, their involvement in research and decision-making is very low. </p>
<p>In most cases (or we can say, always),the value of a house appreciates. So it is an investment and not a spending. Whether it is a small house or a big one, rebars provide strength. What we want to suggest is that people tend to avoid doing the right research for something which may provide appreciation and most importantly, safety to the family. We feel it is high time that end-users become aware of the kind of TMT quality they are purchasing while building their dream home. </p>
<p>While we have given the example of constructing an independent house, even while purchasing a flat or an apartment, we speak about the bathroom fittings, amenities, flooring, etc. No one even asks the builder about what kind of TMT is used while building the whole structure. So, institutional buyers also make a larger pie of the rebars market. Unless home buyers start asking questions, improvement in institutional buying (on quality front) also seems difficult. It is high time that the end-users concentrate on quality factors and make an informed decision, at least for safety purposes and reap long-term benefits. But how would a layman evaluate a TMT bar? There are very simple steps one can follow. Our focus here is to create awareness among the retail space buyers, as they hardly have any expertise on the technicalities. Large institutional players, however, know those factors thoroughly. Further, tiers III and IV cities form a good chunk of TMT markets, where awareness seems to be really low.</p>
<p> <span style="font-weight: bold;">The Revelation: Analysing Test Research </span><br />
While in our storyline, we are speaking about the processes and factors that determinethe quality of rebars, it is more important to make practical analysis rather than simply focus on theories. When we started our research, we thought of analysing a few leading players from the primary as well as the secondary players list. Eventually, we understood the gravity of the subject and decided to undertake the analysis on a pan-India basis. It was difficult to collect samples on pan-India basis due to the weight factor making transportation difficult. To keep the testing facility uniform, collection of samples at one place was necessary. But with a project involving larger public interest, our team took the task with all zest. As the results are now out, it clearly indicates how even renowned players who are spending plenty on branding have failed to clear basic research tests. A good quality rebar should fit into all the chemical and physical parameters stipulated. Failure, even on a single parameter, implies that we are compromising on our safety parameters. </p>
<p>Just to make things simple, we had taken different diameter samples of similar grade (Fe500). Though the classification can be done on diameter basis, a very interesting factor emerged from the test results. While all the primary players managed to get positive results, many secondary players failed on the most common evils (S, P, and S the consequence of skipping the blast furnace process). In the retail segment, usually TMT bars of 8, 12 and 20 mm are widely used and hence, we decided to carry the test on all brands that hold presence in these diameter categories. We added rebars of other diameters as well. However, instead of focusing on different diameters, we analysed, based on brand names and how many of their samples (having different diameter) failed or succeeded.</p>
<p>While all the samples collected from primary players like SAIL, RINL, Tata, JSPL, JSW, and Electrotherm managed to keep the quality benchmark, most of the different diameter samples from secondary players failed to meet the benchmark requirements. Let’s discuss in detail.</p>
<p> <span style="font-weight: bold;">Who Flunked and Who Passed? </span><br />
We see a lot of advertisements from Kamdhenu on the national television. Its 8 and 16 mm diameter samples failed as phosphorous and combinations of sulphur phosphorous were higher than the required quantity. Similarly, we were quite surprised to see a brand like Captain failing to match the quality standards in the 8 and 16 mm. Indo Star did not depict a different story as its 8 and 16 mm diameter samples failed on the phosphorous and S factors. Brands like Majboot failed in 8, 12 and 16 mm diameter segments. SEL too joins the list of brands that failed in three different diameters. Shyam- that advertises with one of the highest paid brand ambassadors- did not manage to pass the P and P parameters. Rather, one of its sample could not pass the yield stress. Brands like Ultrastrong and Fortune failed on at least one parameter. Amba Shakti failed on chemical parameters like phosphorous and S, besides failing on yield stress test as well. Even SRBM failed on both 25 mm and 8 mm samples. It is not that all secondary players failed. A few positive surprises came in from Rathi and Jai Bharat.</p>
<p> For the complete report log on to www.infrastructuretoday.co.in</p>
FlashNews:
Genesys International Q1 Profit Surges 32% on Strong Mapping Demand
Asia-Pacific to Drive 33% of Global Regional Jet Demand by 2045: Embraer
India Achieves 100 GW Solar PV Milestone with ALMM-Driven Expansion
Air India Accelerates $400 Million Fleet Retrofit Programme Across Widebody and Narrowbody Aircraft
ONGC Q1 FY2026 Net Profit Rises 18.2% to ₹115.5 Billion on Strong Gas Realisations and Offshore Gains
Centre Defends Ethanol Blending Programme Amid Mileage Concerns; Highlights $16.5 Billion Forex Savings
Suzlon Energy Reports 62% Surge in EBITDA to ₹5.99 Billion in Q1 FY2026
Inox Green Secures Long-Term O&M Deal for 182 MW Wind Projects
Adani Group Expands MRO Capabilities with Indamer Technics Acquisition
PixxelSpace-Led Consortium to Build India’s First Indigenous Commercial EO Satellite Constellation
India’s Maritime Framework Gets Legislative Boost with Coastal Shipping Bill Passage
IRB Infra and InvIT Projects Post 10% Growth in July 2025 Toll Collections
India Modernises Maritime Laws with Merchant Shipping and Sea Cargo Bills Passed by Parliament
India Sets Global Record with $0.64/kg Green Ammonia Price Under Hydrogen Mission
IndiGo Starts Construction on One of India’s Largest MROs in Bengaluru
SDHI to Manufacture Varex Cargo Inspection Systems in India
Mumbai-Ahmedabad Bullet Train: Sabarmati Bridge Rises to 36 Metres
Tata Power Profit Rises 6% in Q1 FY2026 on Strong Renewable and Distribution Gains
Suzlon Wins 381 MW Order for Zelestra’s First FDRE Wind Project in India
Home » Is India’s Rs.5.7 Trillion Infra Investments at Risk?
Is India’s Rs.5.7 Trillion Infra Investments at Risk?
ECONOMY & POLICY
October 31, 2018June 9, 2021
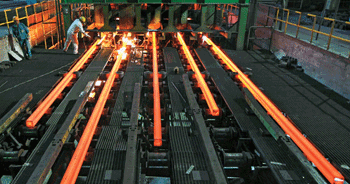
Leave a Reply
You must be logged in to post a comment.